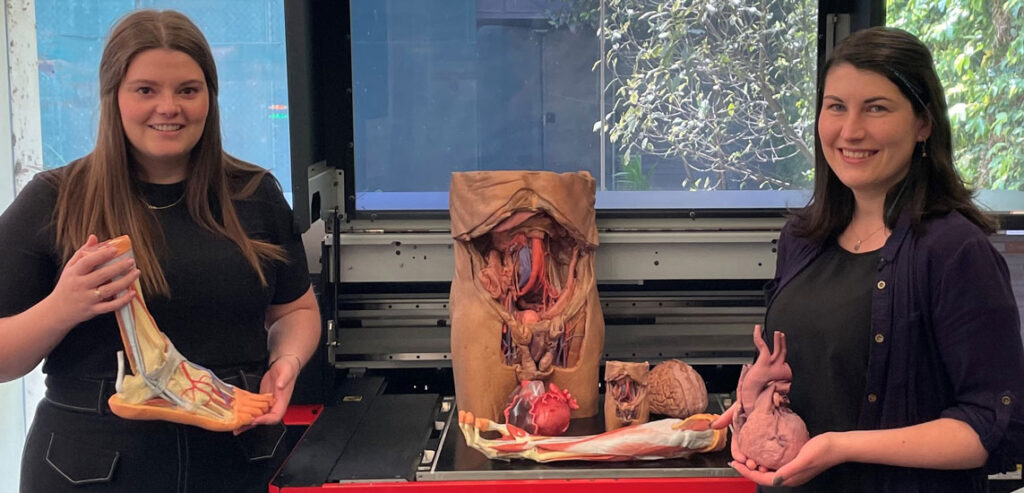
The 3D Innovation and Design Studio, Centre for Human Anatomy Education, Department of Anatomy and Developmental Biology, at Monash University made headlines back in 2015 for its collaboration with German anatomical models’ provider, Erler-Zimmer. The partnership released a set of anatomically accurate 3D printed models that proved revolutionary to the teaching of students across the medical sciences.
While the ‘gold standard’ for teaching human anatomy is the human anatomy itself —historically in the form of cadavers — this age-old teaching tool is fraught with logistical, ethical, and cost challenges. Not to mention the potential for unsettling students just embarking on their studies. Embalming improves the period over which a cadaver can be used, however it changes the natural color and texture of tissues, diminishing the value to future surgeons and doctors.
From a consistency of teaching viewpoint, each cadaver is unique meaning that each cohort of students sees and learns from a slightly different anatomy. Rare diseases can also be difficult to study because of lack of opportunities to examine the specific pathologies. Monash University recognized the opportunity for 3D printing to produce models that were free from the drawbacks associated with cadavers, but retained the anatomical accuracy required for consistent learning outcomes.
Confronting existing setbacks
The first series of models were produced using powder bed inkjet 3D printing, where a binder and color pigment is deposited onto a powder bed (usually filled with gypsum) to build up a 3D model. The powder-based 3D printing process created fragile models, with poor color reproduction that required extensive post-processing to improve strength. This made the process substantially more time consuming than envisaged and the resulting models were lacking in realism and durability. The team at Monash wanted to move into more accurate color representation and models that more closely mimicked the range of textures found in human anatomy.
False coloring of parts is often a good strategy from an educational standpoint: the ‘veins are blue and arteries are red’ standard from textbooks is transposed onto anatomically accurate 3D models, helping medical students starting to consider anatomy fully in three dimensions for the first time. However, the team wanted to also get closer to the realism of the systems they were representing not only in terms of geometries but also coloration. For disciplines like pathology, color is a fundamental diagnostic tool and accurate reproduction is required in any educational models.
User feedback on the first series of models included how fragile the powder-bed parts were, especially when used in the real educational setting with students constantly handling and examining them. Because of the limited size of the print bed, up to 11 individual 3D printed parts were needed to create a single anatomical model. These parts were glued together, which is both time consuming and further impacts the strength of the model, resulting in breakage both in use and in transit.
Gypsum parts are also heavy and larger parts needed to be designed as a hollow shell with holes to release trapped powder. The team found that creating shell structures that were strong enough for the application was a challenge, as was evacuating the powder from the enclosed space. Alternatives to the powder-bed system were therefore sought and trialed, however the high cost of materials and poor color reproduction left the team without a preferred solution — until they saw a demonstration of the Mimaki 3DUJ-553.
Bringing anatomical models to life
After trialing a number of alternatives, the team was invited to see a Mimaki 3DUJ-553 in Sydney and was initially impressed by the accurate color recreation. Further inspection revealed tougher and more tactile final parts straight from the print that could incorporate clear areas providing support or strengthening without impacting the visibility of smaller features.
The 3DUJ-553’s ability to recreate over 10 million colors allowed the team to finally create models with a high degree of visual realism. The team at Monash are able to combine CT scan data overlayed with full-color 3D surface scans to accurately recreate anatomical systems in both healthy and diseased states.
The ability to print in transparent material to show internal structures means that student interaction with the models is much closer to the experience they will eventually have with real human patients. Fine structures such as nerves and blood vessels can be supported and protected with clear material without impeding the visibility. This greatly reduces the chances of breaking during handling and improves the durability of models in a teaching environment.
The large print bed of the 3DUJ-553 allows larger parts to be made in a single piece, and a higher throughput for multiple smaller parts.
Improving teaching opportunities
Adoption of the Mimaki 3DUJ-553 has allowed the team to generate a further two series of life-like anatomical models that would not have been possible with another 3D printing technology.
Models representing rare pathologies, where color and geometry are equally important, are now able to be produced. This vastly expands the teaching opportunities where use of cadavers is either banned on religious grounds, or where the rarity of the diseases means insufficient cadavers displaying the pathology are available to students. Thanks to the larger bed size, models that were previously 11 parts glued together are produced as two parts what are more easily joined. This removes join lines and further improves the tactility and strength of the models.
Accurate printing and strong materials allow for hollow parts with a 3mm shell to be produced. These parts are still strong enough to handle, light enough to transport, but heavy enough to be tactile and pleasing to handle. The quality of the models has attracted attention from across the university campus and across institutions in Australia, with the 3D Innovation and Design Studio team working with many academic institutions, clinical groups, and commercial partners to print pieces generated by 3D capture technologies.
The impact in the university and beyond
Associate Professor Justin W Adams, director of the 3D Innovation and Design Studio at the Centre for Human Anatomy Education explained: “Because we have external commercial partnerships as well as our internal research responsibilities, we have to more cost conscious and offer value to commercial users. Because of that we are more stringent with the relevant calculations on return on investment for our 3D printers than would be the case for a pure research operation. The 3DUJ-553’s quality capabilities — matched with the bed size and reliability — means it has helped tick a lot of boxes for us in that regard.”
Michelle Quayle, Technical Officer at Monash University commented: “We have seen an increase in internal academic interest thanks to the 3DUJ, for example the Archaeology department wanted a Greek bowl printed in full color, paleontologists have asked for some pieces that were full-color surface scanned to be reproduced. People who don’t use a color scanner — for example within engineering disciplines — don’t necessarily want a full color print and will be happier with a single material, it really depends on the technology and processes they used to create their models, but we now have the options.”
Associate Professor Adams continued: “We expect to see growth in the surgical training and surgical simulation areas using the Mimaki technology. Once a surgeon is trained and skilled in a particular operation, especially those that are rarer or more complex, they tend to maintain that skill by performing those surgeries whenever they arise. Meanwhile the next generation of surgeons still needs clinical practice to ensure they have the appropriate skills and training to take over from the current generation of surgeons. So, there is a training crisis — it’s a million dollars to train a surgeon in Australia — and that’s not the salary, that’s just the costs associated with their training. Using highly accurate 3D printed models to train surgeons can help ensure learning isn’t restricted by the number of cases or access to specific pathologies.”