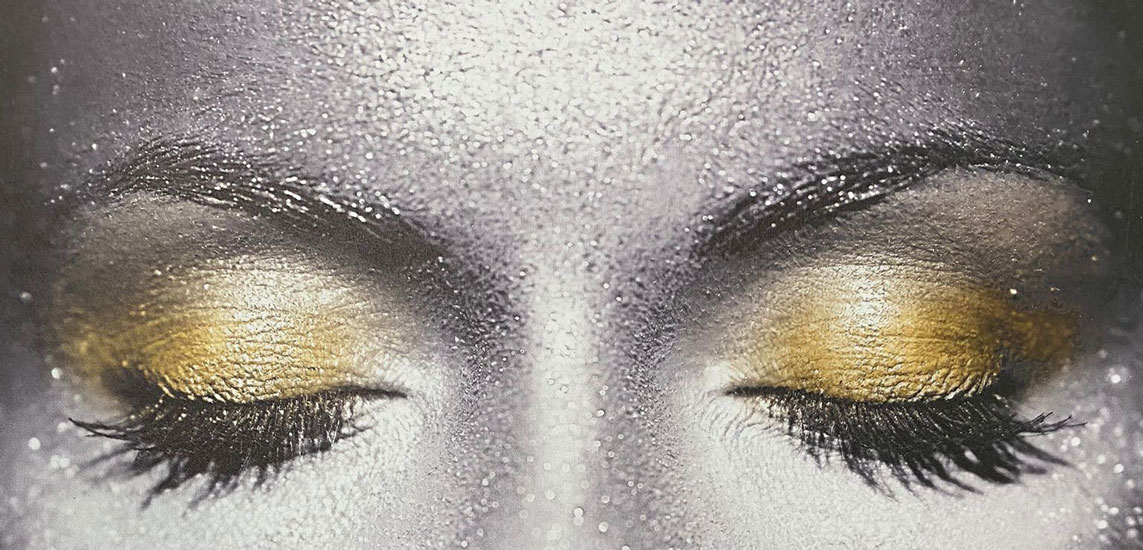
Technologies new and old are helping revolutionise the luxury packaging industry. They allow for printing direct-to-object on any shaped surface or substrate, and in any colour or effect.
The Luxury Landscape
Gold and silver are colours synonymous with luxury and riches. “Worth its weight in gold” and “silver lining” are common sayings denoting the status of these precious metals. They are also common in the realm of packaging to convey a level of status.
The luxury goods packaging industry is a constantly evolving landscape. Yet, everyone knows what to look for when identifying these high-end products. Not only the careful use of these colours, but also the combination of sleek designs, detailed finishes, and impeccable quality, all add to the esteemed “luxury” nametag. The likes of perfumiers, distillers and cosmetic giants, constantly seek different and increasingly efficient ways of providing their consumers with lavishly finished products. Emerging technologies that combine digital printing with traditional padding methods have the potential to provide these packagers with just what they’re looking for.
Many luxury goods come packaged in glass, metals, and other irregular, impermeable surfaces that are notoriously difficult to print on. This challenge has long been recognized as an area in need of innovation. A new application of digital foiling, conjured up in collaboration by the experts at Mimaki and GTO, is the golden ticket for packagers looking to evolve and digitalize their production. It combines newer digital printing methods with the more traditional lamination padding process. Thus, it opens a whole new avenue of accuracy, quality, and efficiency. It offers a new frontier of digital print embellishment.
The Golden Ticket
While having actual gold or silver lining on our favourite products would be truly luxurious – and done by some, using real gold leaf – this is far from cost effective, and impractical in industrial scale production. With this in mind, the best way to convey these colours in packaging is through the transfer of reflective foils.
Mimaki and GTO, an Italian manufacturer of pad printing systems, were able to come together using solutions from Mimaki’s UJF series of UV LED Inkjet printers. This was followed by GTO’s heritage lamination padding machinery. They created a process with which to finish luxury packaging with remarkable accuracy, speed, and new levels of customisability when compared with traditional lamination padding methods.
The first step in the process involves digitally printing a carefully designed primer layer in Mimaki’s UJF-7151 plusII printer. This printer is ideal for printing onto any material or substrate, no matter the surface texture, size, or shape. The printer also boasts extreme image quality and production speeds. Additionally, it applies the primer straight onto the surface of the substrate. This primer acts as a bonding agent, due to its very high levels of adhesion when heated up.
The next step uses GTO’s specialist pad printing machines. Under the pressure of the hot pad, the machine migrates the foil – whether that’s reflective gold, silver, or any other colour or effect – directly onto the product. It only leaves it where the UJF 7151 plusII has digitally printed the primer layer.
So, why is this better?
While traditional foil stamping has been around for decades, what sets this new stamping method apart is the ability to print directly onto irregular surfaces and substrates. Previously, manufacturers could use both hot and cold stamping processes.
For the hot method, a metal stamp, known as a die, is created with a specific design. The die is heated and pressed onto paper with the foil in between. The hot stamp pushes the foil into the paper with an embossed or debossed effect. Although this method resembles the newer approach, each job requires custom stamp plates. This significantly increases the time needed for the process. This also has other drawbacks, such as the inability to print onto irregular surfaces, or risks of inconsistencies in the foiling on the grooves of the design.
Cold stamping foil is a step closer to the new method from Mimaki and GTO. In this method, a glue is applied to the areas on the surface to be foiled. The foil carrier film is then applied on top and put through a pressurized roller. Thus, the foil sticks where the glue is present. While this allows for work on thinner materials than hot stamp foil, and without the need to manufacture a custom plate, again this falls short when it comes to printing on irregular surfaces.
Glass bottles and similar objects, typically used for perfumes or spirits, have differing shapes, curves, and surface textures. They used to be nearly impossible to directly print onto. However, with this new digital process, they can now finish much faster and more accurately. This ultimately cuts costs for the user.
Additionally, with this new digital process, they can now finish much faster and more accurately, which ultimately cuts costs for the user. The possibilities are truly endless. This will allow manufacturers in any industry to start using this process for their luxury packaging.